Navigating the Ins and Outs of Cleated Belting
You are undoubtedly looking for ways to improve your bottom line within your recycling process. Making the operation more effective by speeding up material movement is one way to achieve that goal. A cleated product solution can provide significant value if its role is evaluated carefully during the product development or refurbishment process.
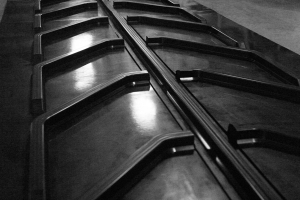
Conveyors running with a cleated belt can often convey material 25 percent faster and achieve steeper angles when compared to standard pattern options (Photo: J. Alan Paul Photography)
Multiple applications operate with standard belt patterns, such as chevron and crescent, to improve upward movement. Although these patterns are workable options, the lack of pattern height loses the fight against the power of gravity. As a result, conveyor equipment is restricted to low inclines. To reach the drop-zone at such a low incline, conveyor systems must be designed at far-reaching lengths. Alternatively, operating with a cleated belt allows you to convey more materials and at higher angles. Here’s why a cleat can create a high-value impact on your business:
What are the benefits of conveying with cleats?
Each type of equipment has an optimal solution for its conveying operation, and using cleats is one way to help yield the highest possible return. One benefit is through increased capacity. Conveyors running with a cleated belt can often convey material 25 percent faster and achieve steeper angles when compared to standard pattern options like chevron and crescent. Using a cleated belt, you could also lessen the roll-back that you experience with a low-profile pattern belt. Cleats hold the material and help maintain forward momentum. In addition, a higher cleat profile and steeper incline provide value by allowing you to reduce the length requirements of the belt and the size of the conveyor system in its entirety. A cleated belt presents the opportunity to shrink the footprint of the equipment and create higher efficiencies in your operation.
What are the different cleat options available?
Industry standards vary, and numerous cleat options are available from a wide range of belting suppliers. What will ultimately give you the highest capacity depends on your application and system requirements. For example, a taller cleat height would be used in applications moving larger materials and at steeper angles to reduce spillage. Cleat shape, angle and design are all relevant to the surcharge angle of the materials you are conveying. With several options and combinations on the market, it is critical to have an open dialogue with your belting provider to learn what will maximize belt life and help lower your total cost of ownership.
How to determine what cleat is right for your operation?
How the belt is manufactured and how the cleats are adhered to the belt, the cleat design, cleat pattern, and numerous other factors all make an impact – positively or negatively – on how your belt performs when conveying recycled materials. Your application and equipment design needs to be taken into consideration when discovering your optimum cleated belt solution. You should source a cleated product that will provide you with the greatest return, and as such, it is difficult to give a straightforward answer to the question of what cleat is right for your operation. What we can do is help educate you on cleated belt fundamentals. That will prepare you and your team to have a discussion with your belting distributor or manufacturer.
What to consider before buying a cleated belt?
- It is important to understand belt fundamentals because the belt you choose impacts your operation’s overall performance, as well as your or your customers’ experience. Here are some tips to make sure you are getting the best belt for the job: Establish your performance requirements (and do not make the mistake of relying on your old spec sheet): If you want to increase belt life and lower your total cost of ownership, your belt provider should help you determine the belt construction specifications based on your performance requirements. The cleats will be irrelevant if you do not start with a proper base. Identifying the optimal combination of fabric, rubber, construction, cleats, and lacing can benefit your system. The best approach to developing an ideal product solution is to open a dialogue with your provider to discuss the conveying requirements of your system as a whole. The right belt construction can provide energy savings, increase roller and bearing life and decrease maintenance costs.
- Determine your cleat profile (size and shape): The recycled materials being conveyed will determine the cleat height, cleat shape and cleat angle. Matching the profile to what materials you are moving and at what angles your system conveys will provide you with the most superior solution. For example, cleat height can be adjusted to reduce roll-back. Nevertheless, there are numerous cleat options available from a wide range of belting suppliers. There are also belt manufacturers, like WCCO Belting, that can engineer a custom cleat profile to support your individual effort to reach peak operational performance.
- Determine your cleat design: What cleat design will work best for you is largely based on the arrangement of your conveyor system. If there is a trough and how much and what kind of edge guards the equipment is designed with, which determines the amount of cleat recess required. Roller diameter will also impact cleat angles and the design. Another consideration is the return roller assembly. Without a smooth return, rollers could cause excess wear and lead to premature cleat failure. And unquestionably, the details of the material being conveyed need to be examined. For example, if you are conveying wet materials and require liquid drainage, the pattern could be structured accordingly to eliminate any interference.
- Determine the ideal cleat frequency: There is a science behind how frequently cleats should be positioned on a belt to give you the best output for your equipment. Your supplier should help you find the sweet spot between the type of product being conveyed, the speed the conveyor is moving, and how often to repeat the cleat pattern. For example, if moving smaller recycled materials in particle-form, the more cleats or buckets, the better, but many factors go into this determination. Make sure you understand why the frequency recommended to you is the best option for your operation.
- Understand how the cleats are adhered to the belt: How cleats are adhered to the belt construction can substantially impact belt life. A belt fabricator modifies premade belting using secondary processes and tools to add cleats. Those tools are, for example, glue chemicals and metal bolts. Did you know that cleats can be bonded through a single-step vulcanization process? WCCO Belting, a belt manufacturer, uses an innovative proprietary process, combining the raw (uncured) belt carcass and rubber cleat extrusions through extreme heat and pressure to vulcanize the belt. The result is one belt that holds equivalent properties throughout and the strongest cleat adherence achievable.
Do not let the same old belt construction (that you may have been ordering for years without question) slow down your progress. Ask your belting provider to present a cleated belt solution based on your performance requirements. If they cannot answer the considerations above, it may be time to consider a new supplier. With the proven increase in efficiency and the positive impact a cleated belt can have on your recycling operation, now is as good of a time as any to see what kind of high-value impact the right belt could have on your business.
(Published in GLOBAL RECYCLING Magazine 3/2021, Page 44, Author: Mike Schroeder, WCCO Belting, Photo: J. Alan Paul Photography)