Maximizing the Economic Value of Scrap Metal
Ecofuturo is a young family-run industrial company. Located halfway between Lisbon and Porto, over the years, it has decided to specialize in the refining of electric motors and small waste from WEEE, to enhance the individual granulated metals.
Owner Guilherme Pina has a clear vision of the future, both in Portugal and throughout Europe. Having moved away from traditional trading activities, he preferred to invest in machinery and technologies to maximize the economic value of scrap metal. In the following interview, you will learn more about Ecofuturo and its collaboration with Panizzolo Recycling Systems.
Can you tell us more about the company’s history?
Ecofuturo was founded in 2014 in Marinha Grande, the same place where my grandfather started his business of collecting and trading metal and ferrous turnings sixty years ago. He was one of the first in this area. We have grown together with companies in the automotive sector, while the second generation has also expanded the field of action to other medium-light scraps.
When I started working in the company, I realized that investing in recycling plants offered greater growth opportunities. The general Portuguese mentality was – and still is – strongly linked to selling as it is, and unfortunately my grandfather’s company made no exceptions. For this reason I decided to change my path and founded Ecofuturo together with my parents and brothers. Right from the start we were able to distinguish ourselves due to our industrial mentality. The path is still long, but we have already obtained positive feedback and we aim to be recognized for the quality of the granulated metals we obtain in output. To date, 60 % of our outputs are sold in Portugal, both to specialized companies and directly to the foundry.
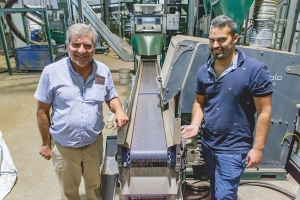
Mr. Guilherme Pina (right) and his father with the copper granule from the Compact Refining Plant (Photo: Panizzolo)
How did you develop the corporate treatment cycle?
At first, we focused on the recycling of electric cables and small WEEE and then, in 2018, we started to focus on the treatment of electric motors. We tried working with Chinese treatment plants. But, the quality of the metals was not what we had expected, the productivity was very low while the breakages were more and more frequent. In those years, we were expanding our presence to the national and Spanish market and, therefore, we wanted to invest in a more performing and professional system.
Why did you choose to work together with Panizzolo Recycling Systems?
I began to understand that the best investment was in the complete enhancement of the copper granulate from electric motors and small WEEE. I carefully analyzed what the European market offered, finding Italian companies very well prepared in this field. Finally, I chose Panizzolo Recycling Systems’ refining plant, as it immediately seemed to be the most suitable for achieving our production and quality goals.
Visiting Panizzolo, I particularly appreciated the transparency, honesty, and experience of Mauro Panizzolo and his team. The company is growing thanks to its direct experience in scrap grinding, learning every day from its grinding processes, and developing the treatment and refining cycles in their plant near Padua. We chose Panizzolo also for the modularity of the elements and the simplicity of maintenance. In the first case this will allow us to quickly install any upgrades, according to our production needs, while in the second case we can easily maintain a constantly high quality of workmanship.
Can you tell us more about the benefits of working with the Panizzolo refining plant?
Before Panizzolo, our refining cycle was based on a Chinese plant that caused problems. For example, the pre-ground from electric motors had to be processed over and over again, discarding many metals before reaching the final output. The production ratio between pre-grinding and refining was low, about 200 – 300 kg/hour, with long periods of storage of both incoming and outgoing material, not to mention any delays due to the turbine being blocked. In the input, there is commonly a percentage of steel, aluminum, and iron, which increased the abnormal wear of the blades, also causing them to break.
Today with the Compact Refining Plant, we can avoid these problems. The refiner hammer mill does not fear the heaviest metals, in a single step, it recovers and maximizes the quality of the metals, saving time, effort, and the operators involved.
How will the future for scrap companies in Portugal look like?
Soon, I expect to see a market increasingly oriented towards waste treatment, with the gradual disappearance of traders focused only on exports.In the coming years, the survival of Portuguese companies will depend on their ability to initiate a path of professionalization both from an organizational and production point of view. The national and European market increasingly wants to structure, organize and modernize waste treatment cycles for the reintroduction of the secondary raw material.
In the next few years my goal will be to expand and consolidate our presence in the Portuguese and Spanish market and, once the plant is fully operational, I do not rule out the possibility of further investing in a Panizzolo hammer mill to improve and implement the cycle of pre-grinding of the scrap I buy.
(GR32020, Page 12, Interview: Panizzolo Recycling Systems with Guilherme Pina, Owner of Ecofuturo, Photo: Panizzolo)