Recirculation with AI: A Second Life for Vehicle Components
Artificial intelligence (AI) plays a central role in the German “EIBA” project.
A huge number of used parts end up in the scrapyard for recycling every year. According to the Berlin-based Fraunhofer Institute for Production Systems and Design Technology IPK, it is more resource-efficient to remanufacture alternators, starters and the like as part of a recirculation approach. This would reduce waste, lower the CO2 footprint and extend the service life of products.
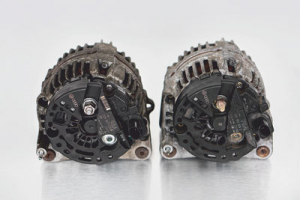
Product variance – two generators with
different part numbers are visually identical (Photo: Fraunhofer IPK/Larissa Klassen)
In the “EIBA” project, the Fraunhofer IPK is developing an AI-based assistance system for semi-automated image-based identification of used parts without QR or bar codes. “This will assist the
worker with the sorting process so that more used components can be sent for remanufacturing.” As stated, remanufacturing – the process of rebuilding used equipment to reflect its original condition – may become a key element of the circular economy.
Four-eyes principle reduces error rate
Identifying and assessing vehicle components is one key challenge in the remanufacturing process. “Many products are virtually indistinguishable from one another and are difficult to identify due to dirt and wear. Up to now, this task has been carried out manually by specialists under considerable time pressure,” the research institute wrote. Fraunhofer IPK‘s AI-based assistance system would help employees to identify and assess defective wear parts such as starters, air-conditioning compressors and alternators based on the four-eye principle.
Identification features such as weight, volume, shape, size and color characteristics are used, but customer and delivery data are also included in the evaluation. The employee, on the other hand, spots any loose components or burnt parts, which is where the AI system’s image processing function comes up short.
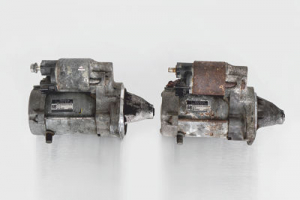
Condition variance – two starters with identical part numbers differ in appearance due to wear marks (Photo: Fraunhofer IPK/Larissa Klassen)
The identification process
At first, the used part undergoes image-based processing, Fraunhofer IPK describes the necessary steps. This would involve the system scanning the packaging to gather information about the product group. By breaking this process down into subtasks, the search range for identification is reduced from 1:120,000 to 1:5,000. The used part is then weighed and recorded by 3D stereo cameras.
As reported, the results obtained from the image-based processing stage are combined with the analysis of the part-specific commercial data, such as the origin, date and location, in order to identify the part reliably. The information is processed by two AI systems simultaneously. “The results of the image-based processing stage are merged with the analysis of the part-specific commercial data, such as the origin, date and location, so that the used part is identified in a reliable and comprehensive manner,” the research institute underlined. Then the outcome of the identification process is shown to the employee, who receives a suggestion list with a preview image and part number, thus retaining full control.
(Published in GLOBAL RECYCLING Magazine 2/2022, Page 38, Photo: Fraunhofer IPK/Larissa Klassen)