Possible Uses of Vortex Layer Systems
According to the author, this technology is suitable for treatment, neutralization and disposal of various waste materials: Vortex Layer Systems is tested and can, for example, improve the quality of wastewater treatment.
So far, there is no scientific and technological achievements which could improve the life of the human race on a global planetary scale. The world is contaminated with trash and hazardous industrial waste; climate change is becoming noticeable. Average temperatures are on the rise, which will eventually cause polar ice melting and flooding of low coastal lands all over the world. Uncontrollable extraction and processing of crude oil is also quite unacceptable.
However, several related technologies, which can address many of the above problems, already exist. These processes were originally suggested in the 1960s by a Ukrainian scientist, D. Logvinenko, but have not received due attention. The idea is based on new ways of influencing matter with energy: a rotating electromagnetic field. This process became the basis of industrial units with capacities two or even three orders of magnitude higher than those of traditional equipment used for the same purposes. At the same time, the energy, material, labor, and capital costs are 5-100 times lower. Process lines based on these systems can be used in just about any industry to great technological and economic effect, without the need to redesign the industry. Logvinenko called his invention the vortex layer system.
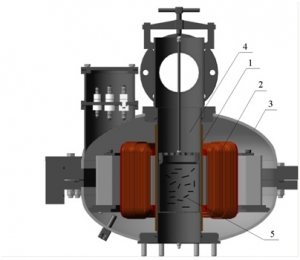
Ferromagnetic particle vortex layer device: 1 – protective collar; 2 – rotating EM field induction coil; 3 – induction coil housing; 4 – non-magnetic operating chamber; 5 – ferromagnetic particles (Photo: Globecore)
The principle of the vortex layer system
A typical vortex layer device uses three-phase industrial electric power to easily generate a rotating electromagnetic field at industrial frequencies, just as it is done in regular electrically powered machines. However, DC static converters, quite accessible now, allow expanding the range of field parameters for fine-tuning the vortex layer system for a specific application.
The design of the device is similar to an asynchronous electric motor – without the rotor. Instead of the rotor, the device is equipped with a chamber. The main component, which generates the rotating field, is a magnetic induction coil, which includes induction core and a three-phase coil. The rotating electromagnetic field is confined within the chamber, limited by the non-magnetic body. The processed material is supplied into the chamber along with ferromagnetic needles, which interact with the rotating EM field.
Chemical and physical processes are intensified due to extremely intensive mixing and dispersion of processed materials, acoustic and electromagnetic effects, high local pressures, electrolysis, etc. All processes occur in the same chamber, in the same mode. Any material can be processed in these units, as long as the particle size (for solid materials) corresponds with the size of the chamber and the needles, liquid fluidity is high enough, and powders can flow freely.
Using the vortex layer devices
One of the most promising directions of the vortex layer application is the processing of waste materials, neutralization, and disposal or recycling of industrial, household, and agricultural waste. Existing traditional neutralization and disposal technologies are inefficient, consuming much energy, materials, and land area. They can also be environmentally hazardous. Calculations show that the complete neutralization of an industrial waste stream with current methods will cost not much less than the production itself and with unreliable neutralization results.
There is a gigantic range of various technology processes and equipment, which perform their function, albeit not fully. The objective is to increase their efficiency without significant capital and power costs.
Now, this is possible. Vortex layer devices have one specific characteristic: They can be retrofitted into existing lines, increasing their efficiency immensely. Thus, quick and simple retrofit is possible to improve waste processing lines of any type.
The efficiency of vortex layer systems has already been tested and proven in the following processes with some environmental impact:
- neutralization and disposal of industrial, household and agricultural waste;
- clearing of small river beds;
- removal of solid household waste, dumps, landfills and wastewater;
- destruction of toxic materials, industrial and agricultural poisons;
- capture, neutralization, and disposal of industrial gas exhaust;
- processing of crude oil and oil products;
- production of biofuel etc.
Now for a more detailed explanation: The vortex layer system is not and should not be thought of as a device that can solve all the global problems mentioned above, which threaten humanity’s continued existence. This system is a tool that accelerates processes and improves the efficiency of existing process lines.
For instance, vortex layer systems intensify and improve the quality of wastewater treatment by high-intensity mixing and dispersion, electrochemical factors, and high local pressures. These factors allow for efficient production of chrome-containing wastewater in one stage in alkaline media (reduction of Сr6+ to Сr3+ and formation of Сr3+ hydroxide at рН 7.5-8.5) instead of a two-stage process (reduction of Сr6+ to Сr3+ in acidic media at рН 2-3 and then formation of Сr3+ hydroxide in alkaline media), greatly simplifying the process and reducing chemical consumption.
The efficiency of heavy hydroxide formation during treatment of acidic and alkaline wastewater in vortex layer systems is due to the formation of metal hydroxides, their co-precipitation and sorption by iron hydroxide, activated colloidal iron which forms due to dispersion of ferromagnetic elements of the vortex layer in the device, due to the electrochemical processes and alkalization of wastewater. Field research in industrial facilities shows that the high degree of heavy metals removal from wastewater (practically complete) is achieved when the pH of wastewater is close to the pH when the corresponding hydroxides begin to form (рН 7.5-8.5), which allows to significantly reduce the time of wastewater decontamination (such treatment in a vortex layer takes seconds, as opposed 15-30 minutes in traditional equipment) and decrease alkaline chemical consumption. It is important to note that the vortex layer process for wastewater decontamination significantly accelerates precipitation of the metal hydroxides in settling tanks (1-1.5 hours, instead of the recommended 2-4 hours), reduces the amount of sediment and its humidity and improves filtration.
The uses of vortex layer systems in industrial wastewater processing reduce chemical use by 1.5-2.0 times and decrease electricity consumption (0.3 kWh per 1 m3 of wastewater instead of 0.6-0.8 kW/h when using mechanical agitators, and 2-6 kWh with electric coagulation methods).
To sum up, the mentioned list of vortex layer system use is far from complete. This technology can be applied in other areas to improve the ecology. Further research is required, of course, and it is hoped that the development will continue.
(GR12020, Page 48, Author: Frank May, Photos: Globecore)