Tire Recycling to Reduce Environmental Impact
State-of-the-art technologies provide full control of challenging chemical recycling processes.
The recycling of end-of-life tires (ELTs) is a real challenge due to the durability of materials and the harm they cause to the environment. And considering the fact that tires are produced in very large quantities, this is indeed a problem of enormous scale. Separating the various materials mechanically within the scope of material recycling and sorting them into different groups (e.g. rubber, steel and textiles) for use in less challenging applications is of course possible. Alternatively, scrap tires can be incinerated in cement plants, pulp mills, or power plants to benefit from their high calorific value. But to keep valuable resources in the loop, the focus should be directed to cutting-edge chemical recycling processes, including those of Pyrum Innovations AG. The company reduces scrap tires to their basic components, thus enabling sustainable reuse.
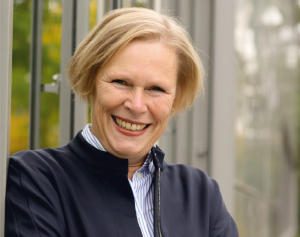
Dr. Frauke Jordt, Head of Chemistry in the Process Automation Business Unit of Siemens AG (Photo: Siemens AG)
Since the 19th century, bicycles, motorcycles, and especially automobiles have been the leading means of individual transport and thus a powerful symbol of personal freedom. The invention of pneumatic tires, which ultimately replaced the bothersome, metal-coated wooden wheels, was a major milestone towards public acceptance. Today, a modern tire is a high-tech product made from rubber, textiles, steel, and various additives. Since the early days of development, tremendous quantities of tires have been produced, used, and finally sorted out.[1]
End-of-life tires are a valuable resource
“These tires aren’t waste, but valuable materials that must absolutely be reused and recycled”, emphasizes Pascal Klein, Founder and CEO of Pyrum Innovations AG in Dillingen: “Through our patented thermolysis process, which is a chemical recycling process, we completely transform the rubber components of end-of-life tires into solid, liquid, and gaseous materials. This process produces so-called recovered carbon black (rCB), an ISCC+-certified, sustainable pyrolysis oil, as well as pyrolysis gas”.
The fields of application for these products are indeed attractive. To mention just a few examples: When used in tire manufacturing or as a pigment in the paint industry, recovered carbon black significantly reduces the carbon footprint of these products. This is due to the fact that virgin carbon black is still being produced in CO2-intensive furnace processes. The pyrolysis oil can serve as a replacement for fossil crude oil for the production of synthetic fibers such as polyester. The use of the recovered oil helps conserve natural resources and thus effectively contributes to climate protection.[2] The gaseous substances are converted into electricity that serves as an energy source for the process itself.
The process developed and implemented by Pyrum is structured in a modular way. It starts with shredding the tires and separating the steel wires and textile fibers from the rubber. Next, the shredded parts run through a so-called vertical thermal reactor[3], from top to bottom, in an oxygen-free atmosphere. This step includes the chemical transformation of elastomers into short-chain, vaporous hydrocarbon compounds and solids. The mode of operation and the process control parameters directly influence how much of each substance is created during this tire decomposition. The pyrolysis oil is the result of subsequent vapor condensation.
A recycling process that produces surplus energy
The remaining, non-condensed vapors consist of a mix of various gases with hydrogen and methane as the main components. This mix is cleaned and converted into electricity in a combined heat and power (cogeneration) unit, thus providing the energy required for the electrically heated reactor. The solid content (coke) is cooled down, ground, and brought to market as carbon black after being converted into agglomerates.
The waste heat produced during this conversion into electricity is used to supply the pyrolysis process and surrounding electrical consumers with process heat. This means that the thermolysis plant is almost energy self-sufficient; only the start-up process requires additional energy. The process even creates surplus energy, allowing the company to also supply other sections of the plant complex. This approach supports the transition toward a sustainable and efficient circular economy, as proposed and requested by the Green Deal of the European Union and the Sustainable Development Goals of the United Nations[4]. Depending on the site concept, the pyrolysis process can save up to 72% of the CO2 produced by conventional thermal recycling.[5]
Modularized processes – holistic digitalization
It is a logical consequence to apply the modular principle to the automation technology that monitors and controls this process, too. Here, Pyrum Innovations relies on automation and digitalization technologies from Siemens that keep the process stable and safe. In addition, the devices installed generate huge amounts of data that can be consolidated and evaluated with suitable applications. Furthermore, this data provides the basis for optimized interventions, for example through parameter adaptation and preventive maintenance. Properly planned maintenance workflows based on actual and accurate asset data enable effective, target-oriented, and perfectly prepared actions. “Thanks to a holistic digitalization concept and state-of-the-art technologies such as the Digital Twin, we benefit in terms of process control, process development, and optimization”, stresses Meike Jungmann of Pyrum Innovations AG.
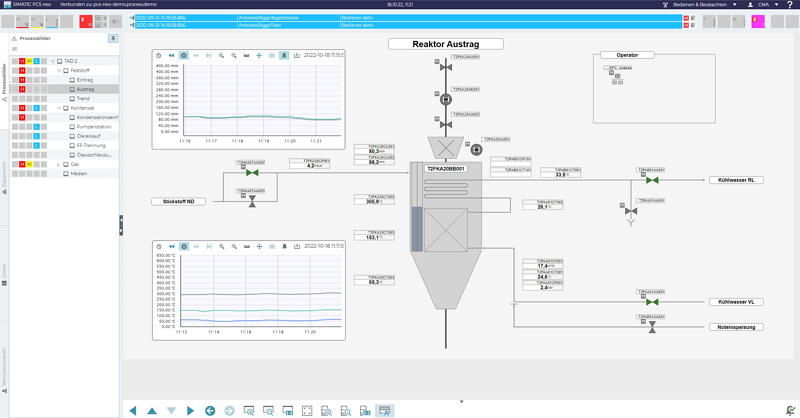
Simatic PCS neo provides access to relevant plant information and helps to securely control and operate the plant (Photo: Siemens AG)
Consistent information in the right context
To extend its existing plant, Pyrum opted for the innovative Simatic PCS neo process control system. Thanks to object-centric data management, all the stakeholders involved have access to consistent and reliable information at any time in order to make the right decisions in the shortest possible time. The Simatic PCS neo provides immediate and secure access to all the information required – independent of the location and time and via all common end devices, including mobile devices. The sophisticated security concept ensures that the know-how is protected against unauthorized access.
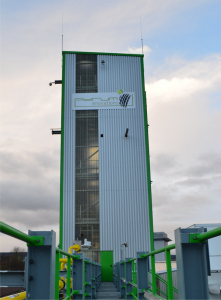
The rubber components of end-of-life tires are transformed into solid, liquid and gaseous (raw) materials in the thermolysis reactor (Photo: Siemens AG)
The system consistently uses state-of-the-art web services. The client requires nothing more than just Windows 10 and an HTML5-capable browser. All the project information is stored on servers on which the licenses and security measures are centrally installed and managed, too. For this, Simatic PCS neo uses cutting-edge IT technology, including secure authentication and communication functions.
Upgrades are installed on the server level, and functions such as control and monitoring, engineering, etc. are available on zero-installation clients. “Web technology also enhances the flexibility and scalability of process control technology. Additional operator stations, for example, can be added within just a few minutes”, explains Frauke Jordt, Head of Chemistry at Siemens. “End devices of various types can be used to access necessary information conveniently and securely, independent of the user’s location.”
Generating added value through industry standards
Compliance with industry standards is a fascinating topic in this context. The field bus technology and its descriptions for standardized communication have already been established on the field level for quite some time. Today, industry is working on descriptions of how machines can communicate with each other. Module Type Packages (MTP) play a major role when it comes to seamlessly integrating plant sections and components into higher-level systems such as Simatic PCS neo.
MTP defines the common “language” for describing the properties of process modules in a manufacturer- and technology-independent way. It thus allows the higher-level, MTP-capable process control system to perfectly control a certain module – such as a shredder or conveyor units.
www.pyrum.net
www.siemens.com/recycling
References:
[1] Goldstein Market Intelligence Global Tire Recycling Market Analysis 2025 https://www.goldsteinresearch.com/report/global-tire-recycling-industry-market-trends-analysis
[2] VAUDE products made from recycled materials. https://nachhaltigkeitsbericht.vaude.com/gri-wAssets/pdf/BPC-2020/FAQs_Recycelte-Materialien_DE.pdf
[3] WO2012092924A1 Thermal Reactor https://patents.google.com/patent/WO2012092924A1/de
[4] Deutschlandfunk archives: Schwerpunktthema Mobilität. Eine Erfindung der Moderne? (Focus topic mobility. An invention of our modern times? – available in German language only) https://www.deutschlandfunk.de/schwerpunktthema-mobilitaet-eine-erfindung-der-moderne-100.html
[5] LCA Pyrum Innovations https://www.pyrum.net/ueber-uns/news-aktuell/news-detail/news/fraunhofer-analyse-bescheinigt-pyrum-pyrolyseverfahren-enorme-co2-einsparungen-gegenueber-herkoemmlich/?tx_news_pi1%5Bcontroller%5D=News&tx_news_pi1%5Baction%5D=detail&cHash=9d8aba10d925982242663948751ba8ca
[6] BlackCycle partners claim ‚world first‘ in recovered carbon black https://www.european-rubber-journal.com/article/2090797/blackcycle-partners-claim-world-first-in-recovered-carbon-black https://blackcycle-project.eu/
(Published in GLOBAL RECYCLING Magazine 1/2023, Page 36 -Advertorial-, Photos / Graphics: Siemens AG and Pyrum Innovations AG)