Tungsten: Multi-stage Preparation Process Allows Upcycling of Residual Materials
Cast aluminum, tool manufacturing and radiation shielding: Newly patented manufacturing process of a tungsten alloy (WNiFe/WNiCu) enables additive manufacturing of complex components.
Tungsten alloys (WNiFe/WNiCu) are used because of their corrosion resistance against molten metal and high thermal conductivity for the chill-mold casting processing of aluminum. But also in tool manufacture and for shielding from alpha and gamma radiation, the heavy metal with its density comparable to gold is indispensable. However, at around 3,400 °C, tungsten has the highest melting point of all chemical elements. Therefore, and due to its Mohs hardness (editor’s note: a scale created in 1822 by German geologist and mineralogist Friedrich Mohs) of 7.5, it is difficult to work with tungsten. As a result, components with more complex shapes, such as curves or conical bores, often have to be switched to hot-work tool steel, which is easier to form. To enable the use of tungsten for those more demanding geometries and thus increase the efficiency and longevity of the components, Bayerische Metallwerke GmbH has developed a new manufacturing process for the tungsten alloys WNiFe and WNiCu and patented it in early 2021. Bayerische Metallwerke GmbH belongs to the Traunstein-based Gesellschaft für Wolfram Industrie mbH. The earlier mentioned process is characterized by the multi-phase mixed crystal alloy that is obtained in a powder form suitable as a starting material for 3D printing and coating processes. Moreover, this powder can be made from scraps or chips, allowing former waste products to be recycled and even upcycled.
“Due to its resistance to corrosion and erosion from molten metals as well as its excellent thermal conductivity, tungsten is the material of choice in the field of cast aluminum,” says Nabil
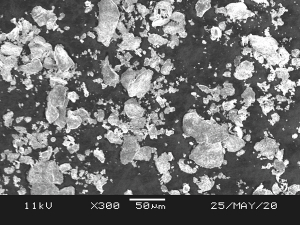
The new manufacturing process is characterized by the fact that the single-phase tungsten-nickel-iron alloy is obtained in powder form, which is suitable as a starting material for 3D printing and coating processes (Photo: Gesellschaft für Wolfram Industrie mbH)
Gdoura, research and development engineer at Bayerische Metallwerke GmbH. “The very high density of 19.25 g/cm3 in its pure form also makes it a good alternative to the harmful lead, which is still used for radiation shielding in medicine, for example.” In the case of casting molds, also known as chill-molds, used in aluminum processing, the aim is often to have long but at the same time very thin and sometimes conically shaped cooling channels of less than one millimeter in diameter to ensure the most uniform and rapid heat dissipation possible. Otherwise, the material quality of the end product can be adversely affected by the formation of cracks. It is impossible to form from the hard and heavy metal, whose extremely high melting point is between 3,387 and 3,422 °C, such precise and sometimes curved shapes using conventional machining or forming processing techniques. Therefore, for these complex components for the purposes mentioned, it has so far been necessary to switch to hot-work steel, which can be brought into almost any desired shape with the help of 3D printing techniques. In contrast, the newly developed manufacturing process by Bayerische Metallwerke enables the difficult-to-machine but durable tungsten prepared for 3D printing. Moreover, the process also allows residues of other processing methods to be recycled as components of the tungsten alloy powder, thus reducing waste and manufacturing costs.
New tungsten alloy in powder form suitable for 3D printing
After completing the two-year development phase, Bayerische Metallwerke applied for a patent for their new manufacturing process for a tungsten alloy product and its further use at the
beginning of 2020, which was granted in January of this year. “The special feature of our tungsten-nickel-iron alloy is that we obtain it in the form of a pre-alloyed powder,” explains Dr.-Ing. Hany Gobran, research and development manager at Bayerische Metallwerke and inventor of manufacturing technology. “This is suitable as a starting product for 3D printing and coating processes.” In the absence of an alternative, only a mixed powder has so far been used to make tungsten usable for components with complex geometries. However, the main disadvantage of such mixtures results from the different melting points of tungsten (around 3,400 °C). But also due to the melting point of nickel and iron since both change their physical state at around 1,500 °C. As a result, a large part of the two added substances evaporates uncontrollably during the melting process in the further processing process. That is because the boiling points of nickel and iron are already around 2,700 °C and 3,000 °C, respectively. Thanks to the pre-alloying during the process developed by Gobran, all three elements are combined as a multiphase material in each powder particle. Thus, their composition and distribution in the end product can be precisely controlled, and no loss of the binder metals has to be accepted.
According to the common standardized variants, the new alloy can be produced with 80 to 98.5 percent (weight) tungsten, 0.1 to 15 percent (weight) nickel and 0.1 to 10 percent (weight) iron
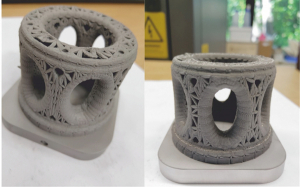
It is impossible to form from the hard and heavy metal, whose extremely high melting point is between 3,387 and 3,422 °C, such precise and sometimes curved shapes using conventional machining or forming
processing techniques (Photo: Gesellschaft für Wolfram Industrie mbH)
and/or copper. That achieves a density of the end product of 17 to 18.8 g/cm3, which is desirable for applications in the aluminum industry, tool manufacture and alpha and gamma radiation shielding. “The higher the proportion of tungsten in the end product, the more resistant it is to molten aluminum and the better its thermal conductivity,” explains Gobran. “If, on the other hand, good ductility and mechanical machinability play a greater role, the proportion of tungsten in the alloy can also be reduced accordingly. The composition can therefore always be adapted to the specific application and the respective complexity of the shape.” During the comminution process as part of the manufacturing process, the flow behavior and the grain size of the powder between 10 and 200 µm can also be determined. In this way, the alloy is individually prepared for the desired type of further processing – such as plasma coating processes or additive manufacturing.
A new manufacturing process enables materials to be upcycled
If, for example, the hot-worked steel previously used for thin and conical cooling channels in cast aluminum chill-molds is replaced by the tungsten alloy developed by Gobran, the application benefits not only from the heavy metal’s resistance to corrosion and erosion. Compared to steel, tungsten also has the advantage of much higher thermal conductivity so that the wear on the chill-molds can be massively reduced. Due to its higher density, the alloy product is also an alternative to poisonous lead. That is used not only for radiation shielding but also as a stabilizer, for example in the tool industry. “Another special feature of our alloy is that we can make the powder from scraps or chips,” adds Gdoura. “This is a big step forward from both an economic and environmental perspective, as it allows us to recycle and upcycle waste products from conventional processes.”
(Published in GLOBAL RECYCLING Magazine 3/2021, Page 12, Photo: Gesellschaft für Wolfram Industrie mbH)